A Day in the Life of Alexandre Leroy
Planning Manager Le Sayec Hatchery
I started working at Le Sayec Hatchery in 2006 as an incubation assistant, alongside the incubation technician. Here I was able to learn and understand the importance of hatchery maintenance and control environmental conditions like temperature, hygrometry, and airflow, which are all essential for optimal poult performance.
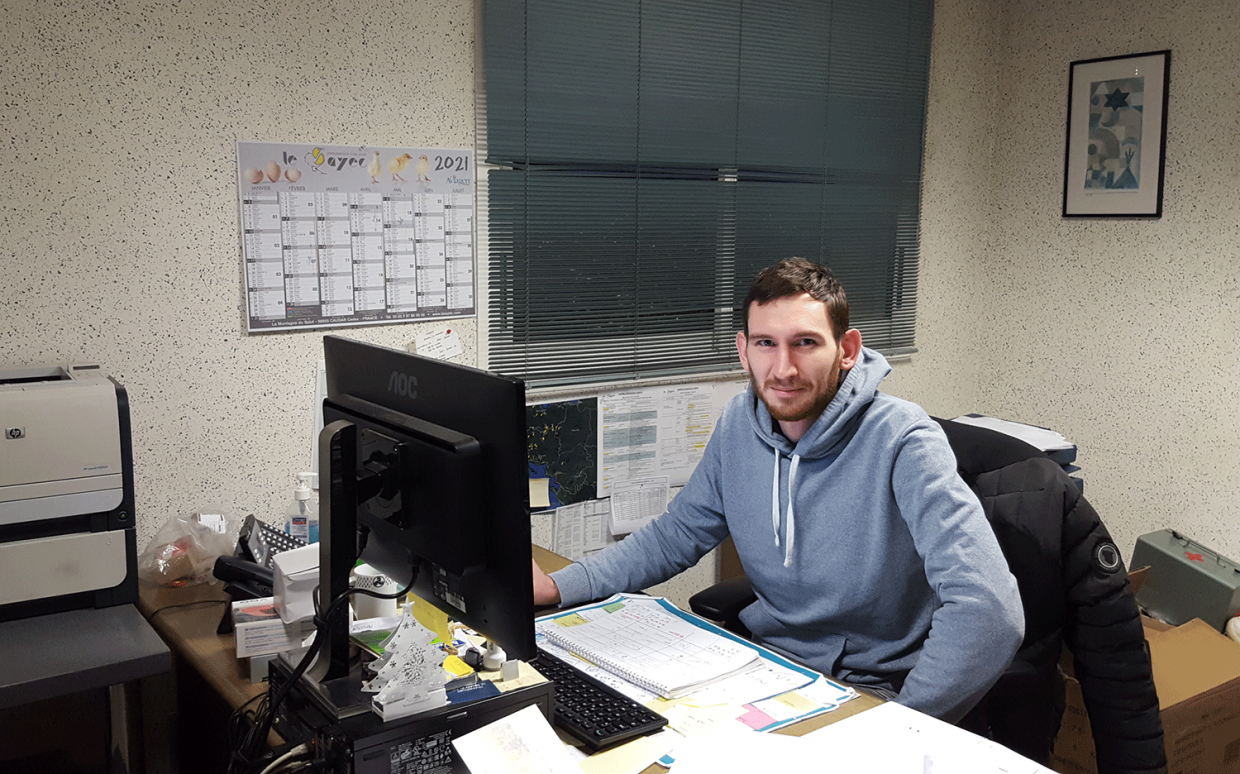
Later I joined the logistics team as a logistics manager, preparing for and shipping day old turkey poults, including; hatch, selection and vaccination. I also assisted my colleague, Gilles Stephan in scheduling egg collections and deliveries.
In 2016 I was given the opportunity to take over from my colleague Gilles, who took the on responsibility of sales planning. I now plan all logistics around eggs and day old turkey poults including; egg collecting, flock selection for day old poults, shipment and liaison with our customers.
We export 250,000 eggs and hatch 240,000 poults per week, so this is highly dependent on effectively communicating with our customers for any requirements and to plan their delivery.
In collaboration with the incubation technician, we do our utmost to have an irreproachable quality of turkey poults. We monitor and record all incubation and hatch figures; including % of infertility, % of hatch and all incubation settings.
Studying engineering at school taught me perseverance and to never stand still, always improve yourself and keep learning. My function is a central pillar of the hatchery operation and is not always easy but I love the challenge every day. Good performance is not possible without motivated employees, for this reasons we manage them like a family and listen to them.
With my 15 years of broad experience in the Le Sayec Hatchery, the experience of my colleague Gilles and now Jerome Noirault at the head of the Le Sayec team, we can offer the best poults for our customers.
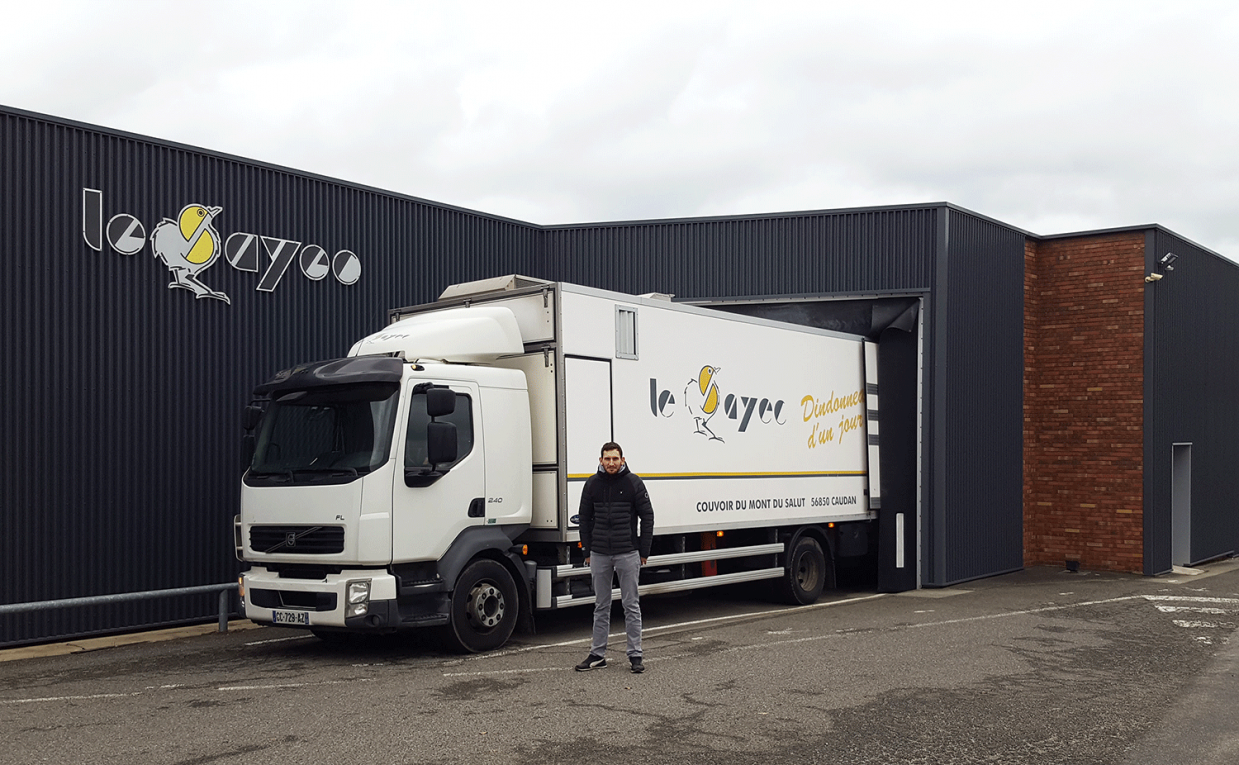
A typical day for Alexandre
Wake up at 5:00 am, first thing to do: check my phone! After a good breakfast, I arrive at the Hatchery at 6:00 am. I start with a short briefing with my assistants to check all employees are here and discuss the hatching day ahead and status of the poults which hatched the night before.
I then check my emails and enter the hatchery around 8:00 am to welcome the incubation staff. Next, I take a little walk around the hatchery to see if anything requires my attention.
Once back at my desk, I prepare the schedule for next hatching day, then by phone and email I contact customers for their delivery next week. Meanwhile lots of poults are being prepared for shipment; we establish a delivery note with the flocks, which allows traceability of the batch for each customer.
For the rest of the morning I focus on upcoming orders weeks in advance and my colleagues send the plan of egg deliveries so I can prepare the logistics for collecting eggs and delivering the daily batch. Transport efficiency is one of our top priorities; for this we have a small fleet of 6 trucks and 2 vans in which we control the temperature and airflows settings.
Until lunch time, I also managed the egg collection and incubation for the day.
Once my drivers return after their pick-up and all batches are shipped, I take a break for to my mind.
In the afternoon, I take care of hatch forecast, hatchability, quality of poults, mortality and customer’s feedback. I speak with our incubation technician and maintenance if correction is necessary.
We export eggs in the afternoon, in which health certification is required for proving our animals are in the best of health. Before my departure, I take another tour of the hatchery to see if all is well for the next days hatch and at 16:00, it’s time to go to home.
Customer satisfaction is our priority. The job is hard work but very interesting.