Warm Weather Ventilation Management
A poultry house ventilation system is arguably the most important management tool for a farm manager to use. As the birds grow and climates change the system needs to be able to adapt and cope with the changing demands to keep the birds in their comfort zone which ensures optimal biological performance. During the periods of hot and/or humid weather, it is essential that we provide the birds with cooling.
This will be provided through the “wind-chill effect”, which is created by air movement and evaporative cooling. The only way to determine if the ventilation system is set correctly is to look at bird behaviour. Always use climate control systems as a guide and never the sole gauge of a turkey houses suitability for bird comfort. If bird behaviour indicates that changes to ventilation are required, those changes should be made swiftly to ensure birds are kept as comfortable as possible.
We need to remember that the actual temperature felt by the bird is influenced by relative humidity (RH). So, for a given temperature, if the RH is low, the birds will feel cooler than if the RH is high. A high RH reduces the bird’s ability to lose heat via evaporative loss or in other words “panting” so we must then lower the ambient temperature to account for RH.
Tunnel Ventilation
Tunnel ventilation should be a secondary measure for when transitional ventilation is no longer keeping the birds in their comfort zone. In general, the exhaust fans are located at one end of the building and at the other end two large openings where the air is drawn in. When the tunnel ventilation is operating, air is drawn along the length of the house at speed. This air flow creates a wind-chill or cooling effect on the birds so that they feel a lower temperature.
It’s important to exchange all the air in the house frequently to minimise the heat build-up. If the air exchange isn’t on a frequent basis, then there will be a vast temperature difference between the front and rear of the house. Another problem of the air moving too slowly down the house is that it not only picks up heat but also contaminants like dust, ammonia and humidity.
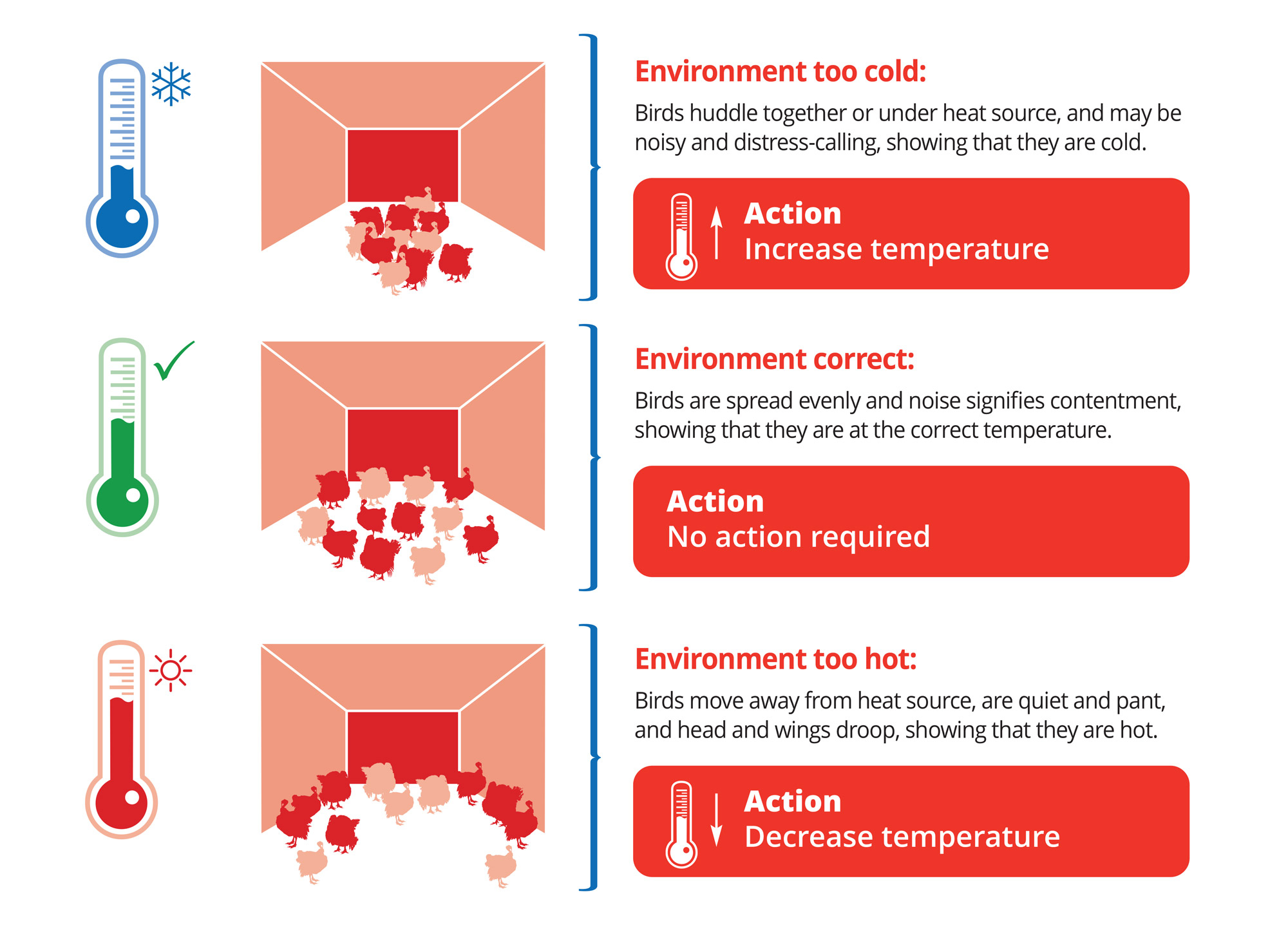
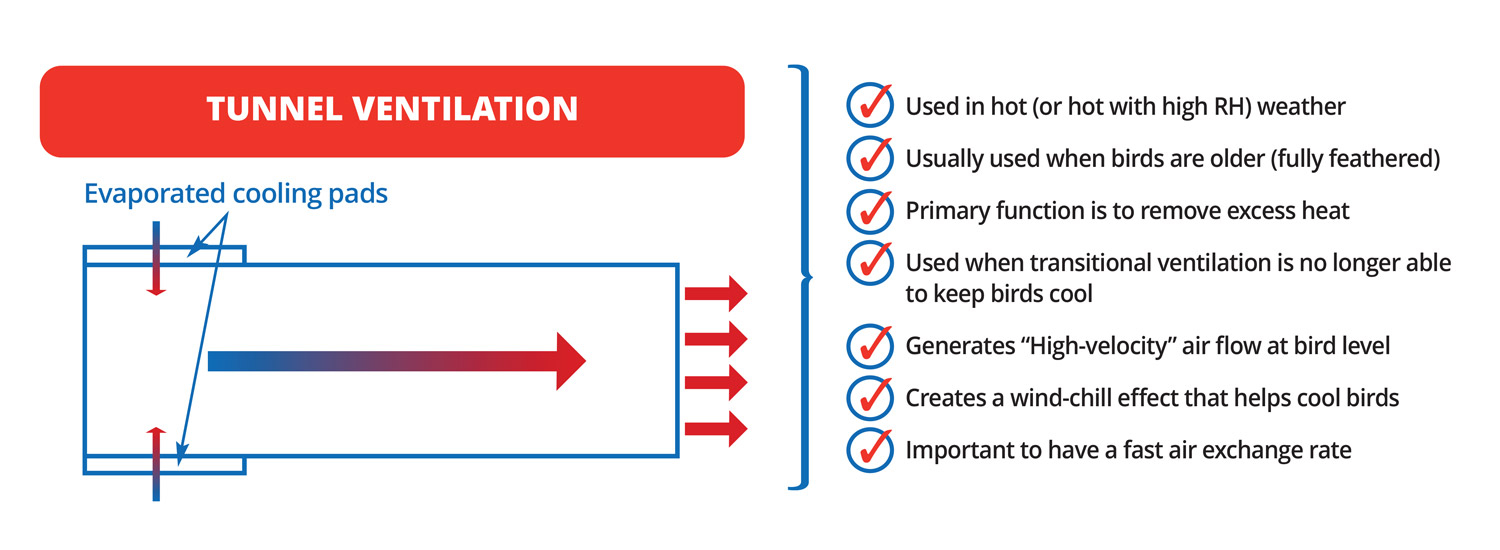
To avoid this the system should be capable of exchanging all the air in the house within 1 minute. The equation to work outhow many fans we would require is to divide the volume of the house by the air exchange time (1 minute).
It won’t be necessary to exchange the air this quickly all the time but a ventilation system should be able to deal with all weather conditions including the warm/humid temperatures during the summertime. It’s also important to note that if the temperature isn’t high enough to run at least half of the exhaust fans, then the transition ventilation should still be utilised.
Another area to consider when using tunnel ventilation is how quick the air will move (air velocity), as this provides most of the cooling. Cooling produced in this way is typically referred to as the “wind-chill effect”. It is hard to determine exactly what temperature a bird feels when the air moves at a certain speed as there are a lot of variables. However, designing a tunnel ventilation system to reach at least 2m/s of air speed, should give a rough ‘wind-chill effect’ of 5ᵒC. Air velocity can be worked out by dividing the total fan capacity by the cross-sectional area of the house.
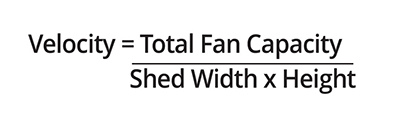
A great way to increase the speed of air when using tunnel ventilation is by using air deflectors. These are installed from the ceiling to the top of the sidewalls, which reduces the cross-section area of the house. This temporarily increases the air speed under each deflector and if the deflectors are positioned no more than 10 meters apart, the increased velocity becomes very consistent all the way along the house. Air deflectors are a great way to increase air speed at a minimal cost.
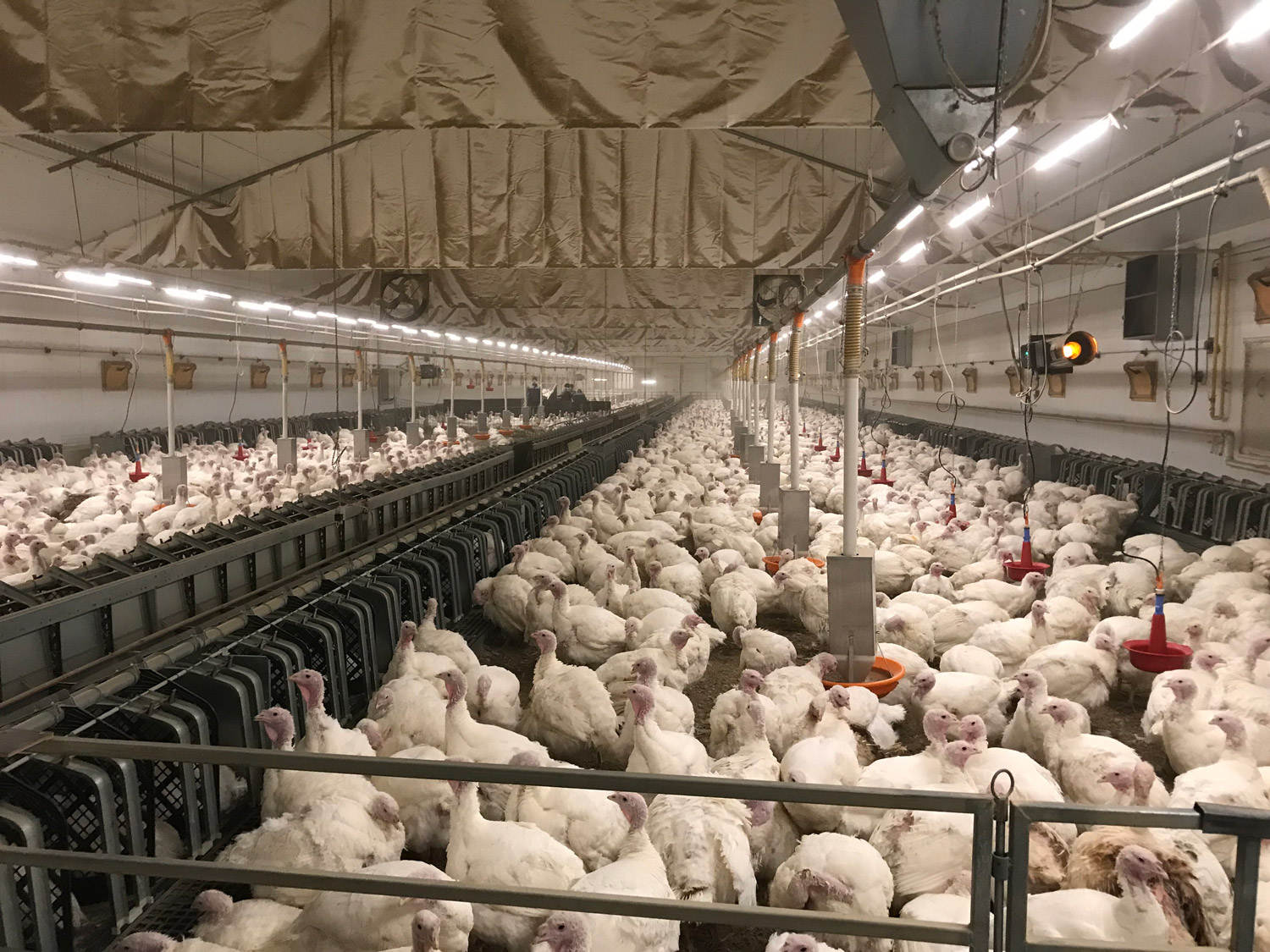
It’s critical to ensure the inlet opening is not open too much or too little, as this can have an impact on both fan performance and bird production. The total inlet space will depend on whether the air is being drawn through cooling pads. In general, for a 15cm (6inch) pad there should be one square meter of pad for every 6,400mᵌ/hr of exhaust fan capacity. For houses without cooling pads, its generally equal to the cross-section area of the house, width x average height. For example, in a house with a width of 15 meters and an average height of 3 meters, there would need to be 45m² of inlet area. It is worth noting that inlets should be placed on either side of the house or across the gable end as this will ensure the most uniform and efficient air movement.
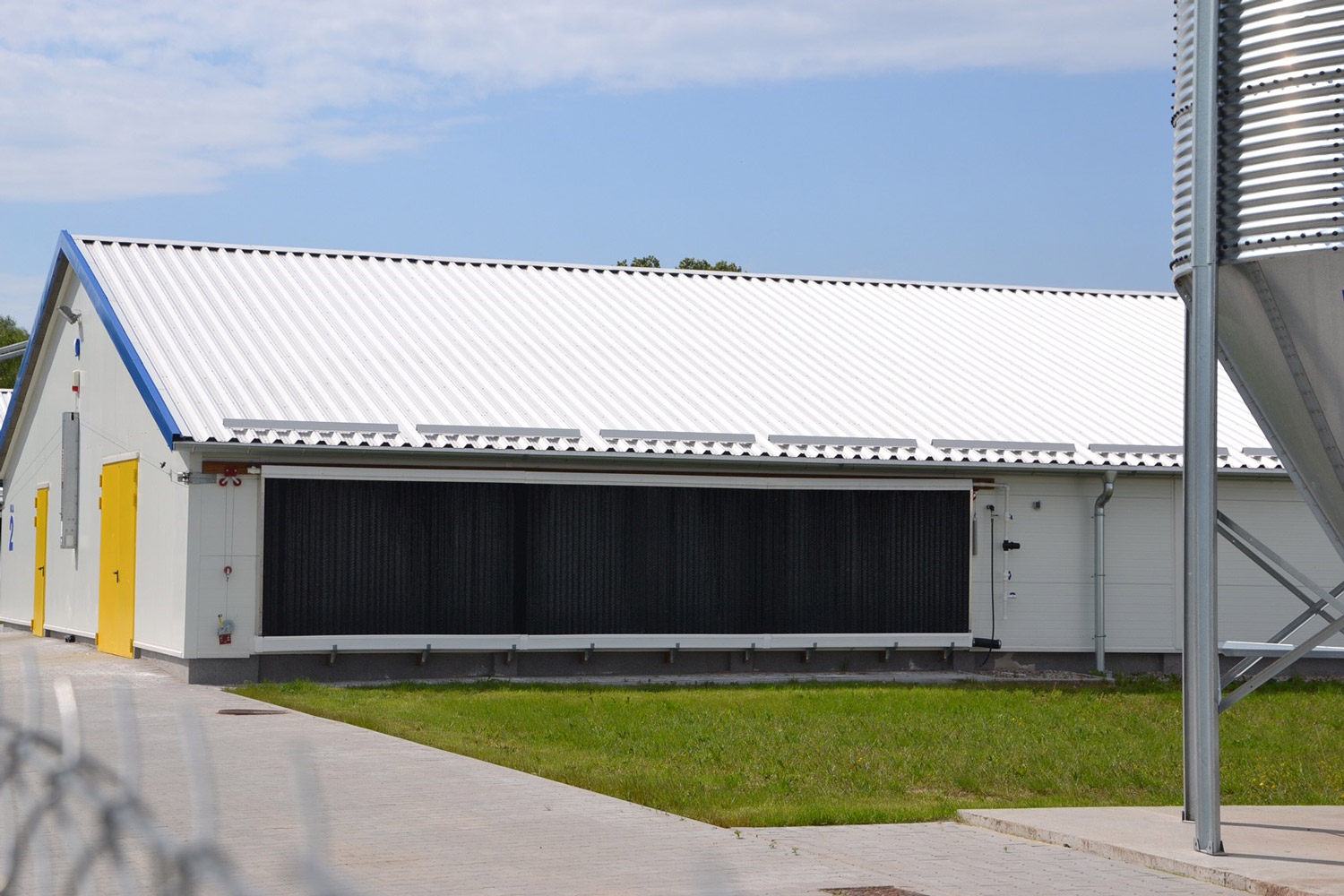
There are a couple of things to keep in mind if including a misting system in a poultry house to guarantee maximum evaporation of the water, these include droplet size and nozzle placement. Misting lines should be placed near to the air inlets of the house and close to the ceiling, as this maximises the time the water droplets are kept aloft in the air. This is important as the greater time it is kept in the air, the more evaporation can occur which increases cooling. To ensure that the droplets are kept in the air as long as possible its important to make them as small as possible. The size is determined by two things, the size of the nozzle and the water pressure. So, the smaller the nozzle and higher the pressure of the system makes for a smaller and more effective droplet size.
Furthermore, in every case you should refer to the manufacturer’s guidelines and recommendations for your own situation. Please see Aviagen’s “Essential Ventilation Management” booklet for a more detailed description of ventilation management.
References
Aviagen (2019) Essential Ventilation Management
The University of Georgia (1990) The Design and Operation of Tunnel-Ventilated Poultry Houses